Tungsten carbide cutters for work on non-precious metal: Why it is worth the change:
Tungsten carbide cutters, or rather, rotary instruments in general are part of the dental technicians daily routine. “We need high quality products that support us during our work and reliably deliver good results”, says dental technical Christian Schuchmann (Manager of the dental laboratory Teuber in Darmstadt, Germany).
At our laboratory, we work a lot with non-precious metal. For removable dentures, we prefer using a tried and proven non-precious metal in most cases, whereas about 70 % of fixed dentures are completely made of ceramics.
Yes, definitely, but non-precious metal alloys are still a firm part of our work. Interestingly, the demand for telescope supported dentures made of non-precious metal is currently growing, often in combination with implants. That’s why we still need tungsten carbide cutters, and we are pleased to note that Komet is currently developing new, innovative instruments in this sector. We have been working for more than six months with the new tungsten carbide cutter SHAX which enabled us to once again optimize our work processes.
… both. We have been producing fixed restorations according to CAD/CAM supported methods for approx. 20 years, including restorations made of non-precious metal. We now have a relatively large stock of machines and enjoy making use of digital technologies. Likewise, we are successfully using CAD/CAM systems in telescope technique and we have developed some milling parameters that produce an excellent fit between the primary and secondary part. In some cases, we proceed according to casting technique, for example when processing model cast work pieces. We use selective laser melting processes in some cases – which we outsource to external service providers, although we also cast our own frames, depending on the situation. But whatever production method we apply to finish the framework quickly, we always need high-performance tungsten carbide cutters.
We have been working with SHAX for more than six months now. As Beta users, we have the opportunity to already test a new cutter while it is still in the development phase. We have been enthusiastic Komet customers for a long time and we could not wait to see this new cutter. We wish to improve the work flows in all areas of our laboratory, so we were pleased to accompany the test phase and we were not disappointed.
No, we were very happy with the “old“ tungsten carbide cutters made by Komet, but as an innovative dental laboratory, we are always on the lookout for new materials and optimized tools. We just wanted to find out more about the advertised “Revolution in work on non-precious metal” and therefore decided to give the new cutters a try. We have been working with Komet tools for many years and we just wanted to know if there is still room for improvement when it comes to trimming non-precious metal frameworks.
… a considerably better feeling during milling. The “notably improved substance removal“ advertised in the brochure is not just a marketing slogan, but reality. The cutters have an amazing ability to remove substance and they create much smoother surfaces. This is what distinguishes SHAX from any other tungsten carbide cutter we know. Working with this instrument is such fun. Milling feels as easy as child’s play because we need a lot less contact pressure to achieve a good result. You just let the cutter do all the work. This is not only gentle on the wrist, but also reduces the wear and tear of the laboratory hand piece. SHAX allows relaxed and efficient work – perfectly in line with our ideas of modern dental technology.
Yes, we do. We have been using the SHAX cutters for non-precious metal restorations ever since we introduced these instruments at our lab. Whether rough trimming or fine grinding – with its many different geometries, there is a SHAX cutter for every situation. The smaller geometries, for example, are perfectly suited for precise work on the inner surfaces of clasps and clasp shoulders. The larger geometries facilitate a tidy removal of casting sprues.
The distinguishing feature is the special blade geometry of the SHAX cutters. We had enquired about this beforehand and we find the background of this instrument very interesting. The new toothing is the product of a special production standard. Just like in dental technology, the technologies in tool making are subject to constant change. The product of SHAX cutters is based on the geometric data of a 3D model. That’s why the SHAX blade geometry cannot be compared to that of other tungsten carbide cutters. It is distinguished by the individual height, depth and angle of each tooth. According to the manufacturer, this improves the cutting behavior of the instrument. This is confirmed during day-to-day work by the dynamic and effective substance removal of the instrument and by the perfectly smooth surface finish created. The resulting finish is considerably finer so that the time required for polishing can be significantly reduced. Thanks to the perfectly prepared surface, we can achieve a mirror finish in record time by polishing with rubber polishers and polishing brushes.
Definitely. At the start, we all focus on the quality of the result, and SHAX cutters really do achieve brilliant results every time. After a few months of use, another advantage becomes obvious. The new cutters last considerably longer than traditional non-precious metal cutters. Even if the instrument is subjected to heavy use, there is hardly any visible wear and tear of the blades. This makes them economical and cost-effective in use. You get more of a tool at the same price, if you like. In summary, we can work with the cutter for a longer period of time, we achieve a finer surface finish and we have great fun during work. For us, the change was definitely worth it.
… Quality, innovation and reliability. The tools made by the company simply work well. Whether diamond abrasives, tungsten carbide cutters, polishers or separating discs – the products are reliable and safe.
Thank you for the interview.
Annett Kieschnick, Berlin
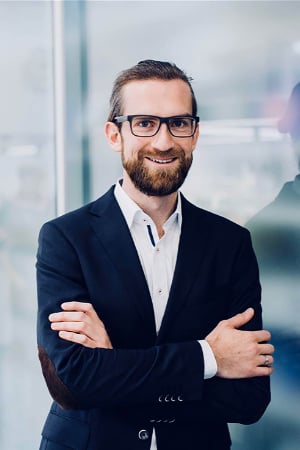
Christian Schuchmann and his colleague Hans Jürgen Lange jointly manage the dental laboratory Teuber in Darmstadt, Germany. The laboratory focuses on modern dental technology consisting of digital technologies, craftmanship and services.